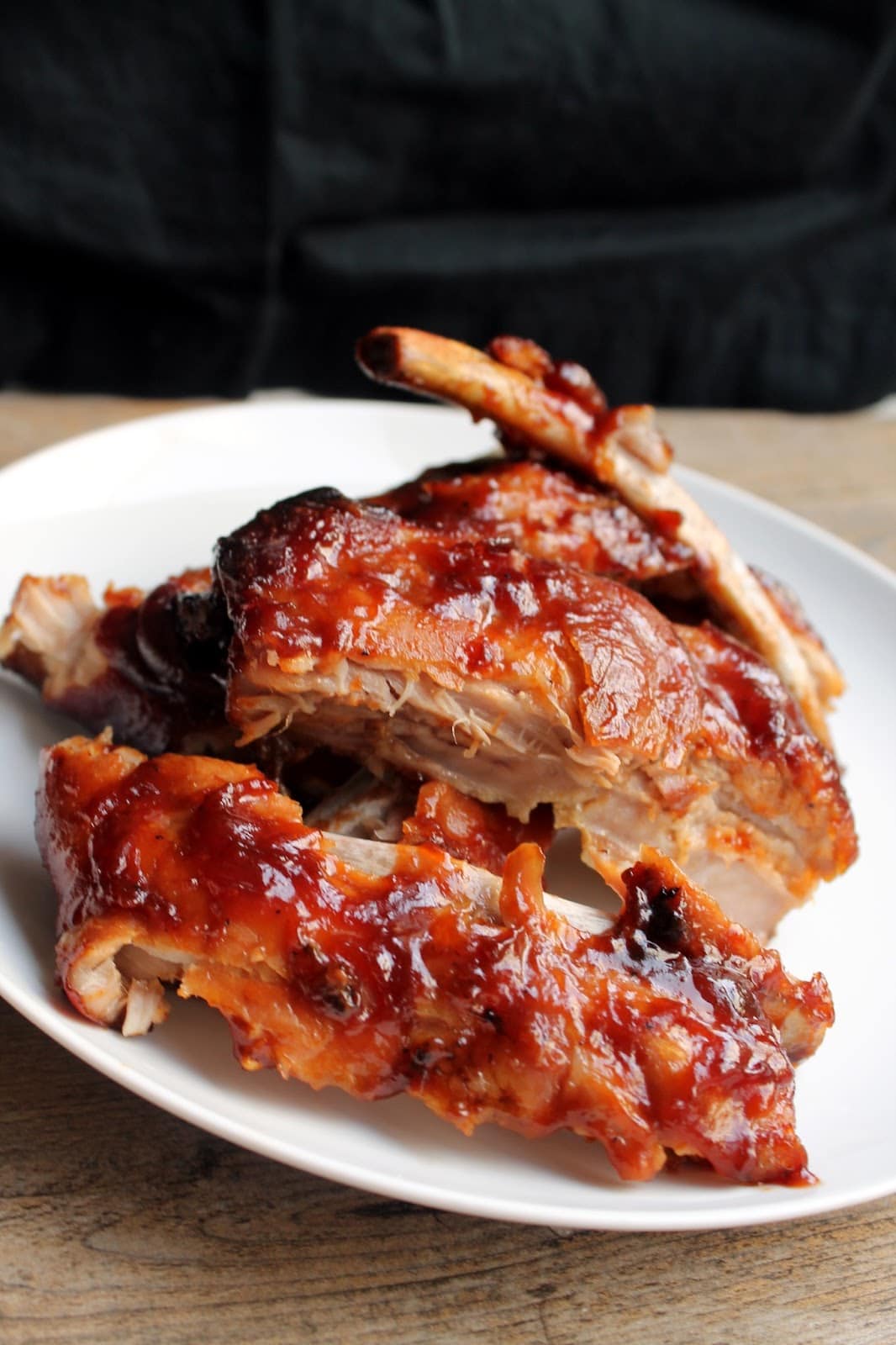
The Secret to Crockpot Ribs (Slow Cooker)
Plastic Part Design Fundamentals Ribs and Bosses Rib Design. Ribs are a great way to add strength and stiffness to a part while keeping material consumption to a minimum. However, a word of caution: ribs can cause sink marks to develop where they intersect the main wall. A rule of thumb to follow is the rib thickness should not exceed 60% the.
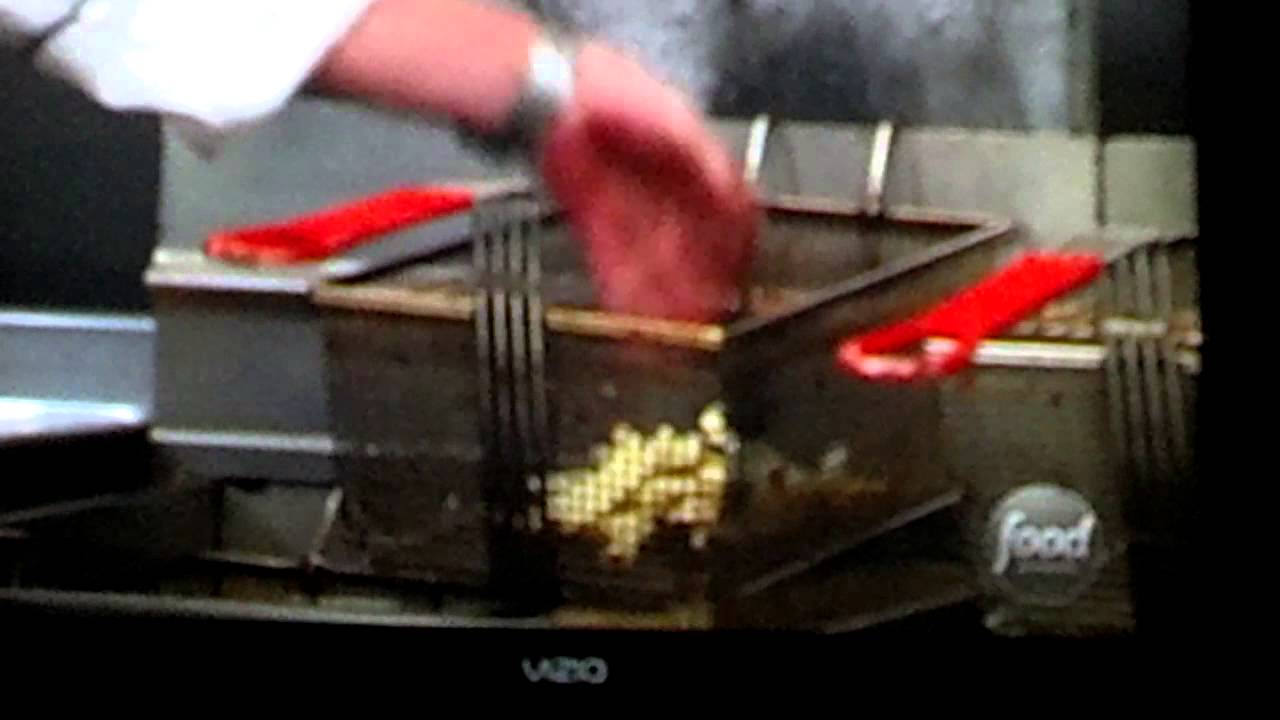
Ribs in plastic wrap YouTube
SOLIDWORKS has a plethora of tools for designing and modeling injection molded plastic parts. This series of video tutorials will cover workflow and modeling.
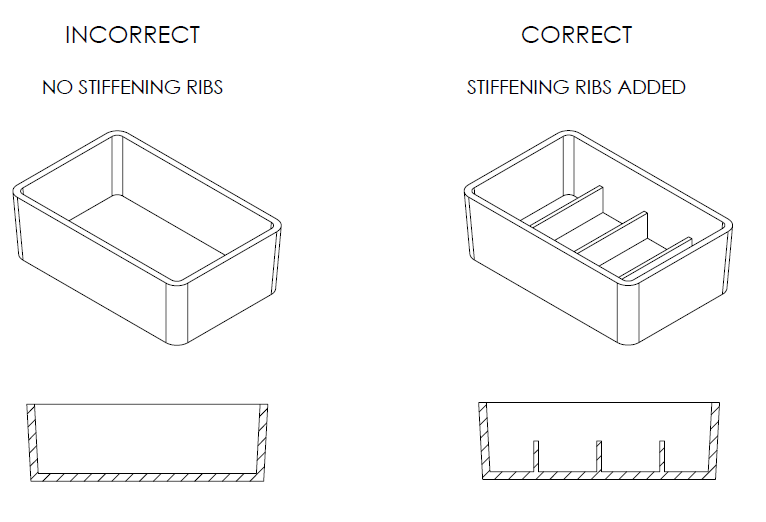
Stiffening ribs Best Plastic Molding Parts Service in China
Depending on the plastic material property used, the rib thickness is suggested to be 40% ~ 75% nominal wall thickness. Rib Radii. It is suggested to include a radius where the rib meets the base or sidewall. This reduces stress concentration, boosts rib strength, and makes smoother plastic material flow when plastic injection molding.
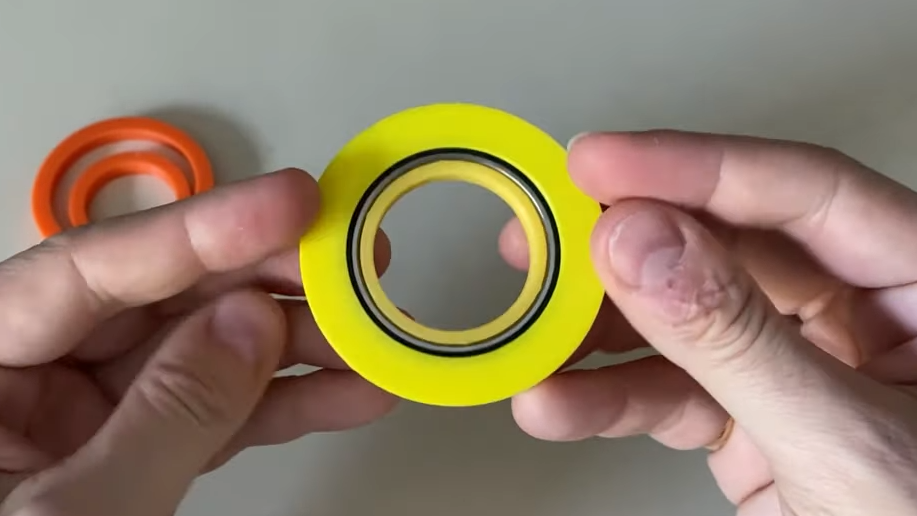
Adding Crush Ribs To 3D Printed Parts For A Better Press Fit Hackaday
Rib Design. As with many features for plastic parts, rib design guidelines that have been developed through years of experience recognize the constraints imposed by practical processing and appearance considerations. For example, a properly proportioned reinforcing rib will be thinner than the nominal wall to which it is attached. If the rib is.

Roman Shade Plastic 1/4" Ribs (5 ft.) Sailrite
Plastic rib design is paramount to the success or failure of the overall product. Some crucial guidelines for designing crush ribs are as follows: The fabrication process of the rib must be carefully considered during design. To reduce sink marks and warp, the rib should be as short as possible while providing the required stiffness.
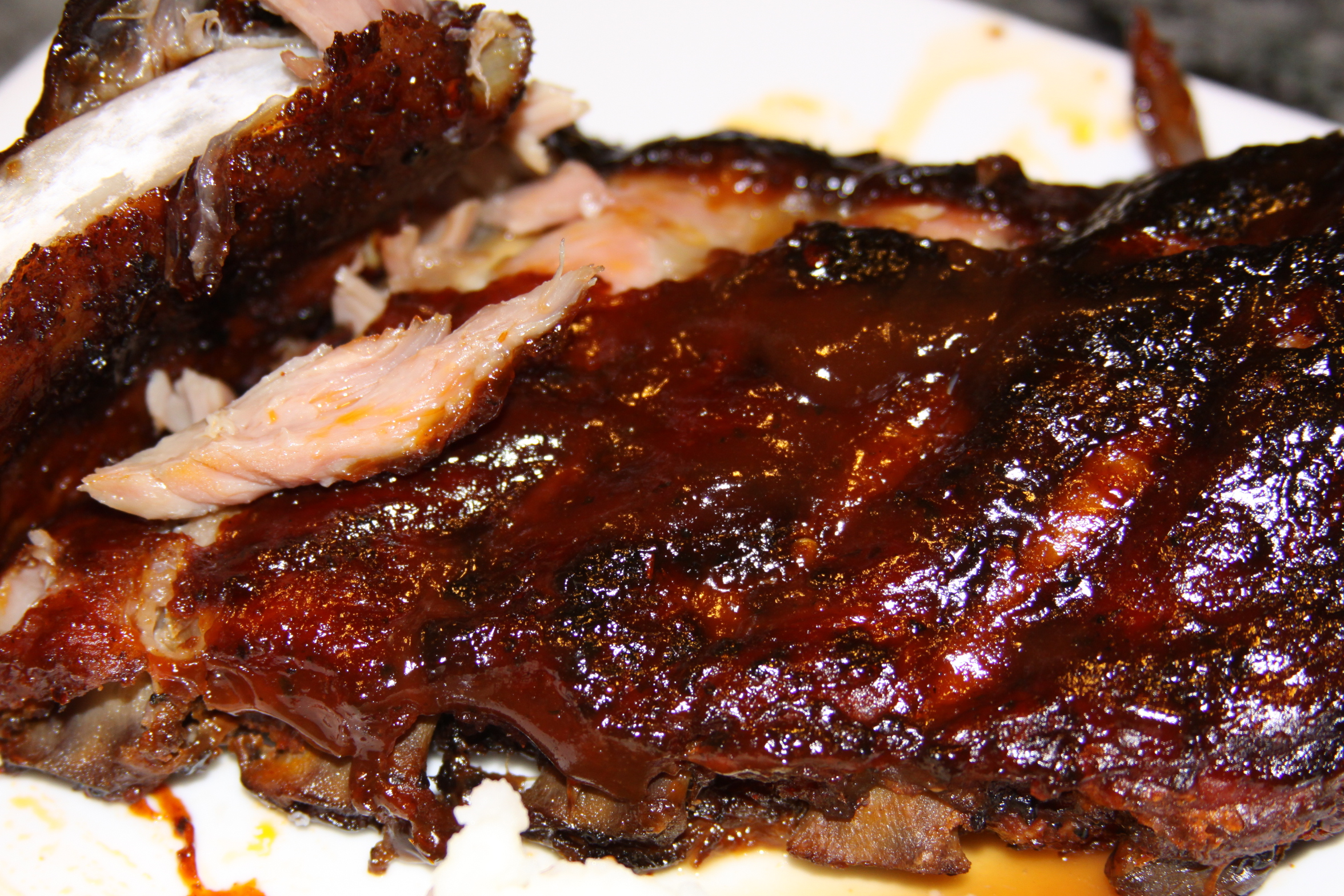
Another crock pot gem BBQ Baby Back Ribs The Lady 8 Home
When designing plastic components, it's often necessary to add ribs and gussets to improve the stiffness and strength of load-bearing features. This reduces material volume and optimizes print time for 3D printed parts, since it takes longer to make these features solid structures (print time is largely driven by the volume of material for a.
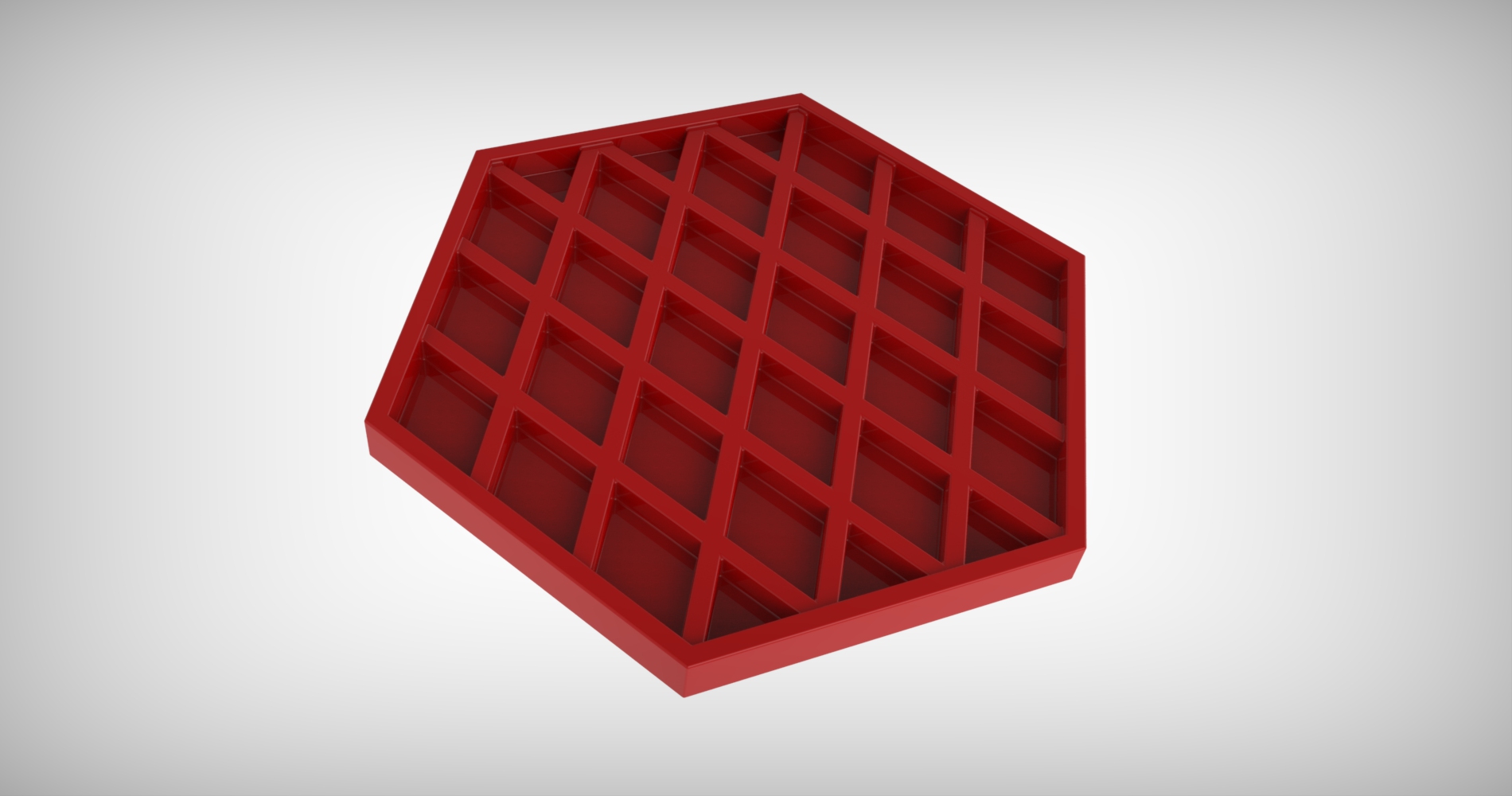
FAQ Rutland Plastics
Want to learn more about Ribs and Gussets? Visit https://jayconsystems.com/blog/considerations-when-adding-ribs-and-gussets-to-injection-molded-parts
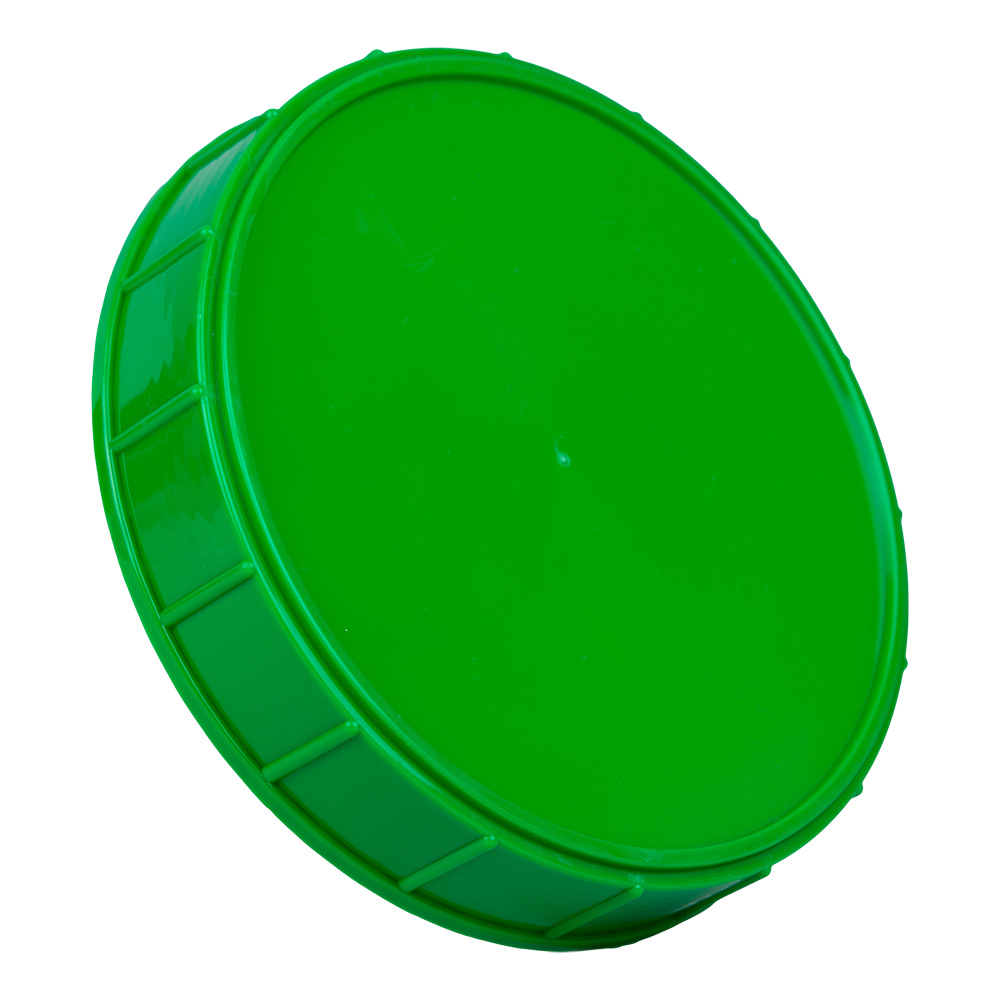
120mm Green Polypropylene Coarse Ribbed Lid U.S. Plastic Corp.
Ribs should be spaced a minimum of two times the nominal wall thickness apart from one another. Rib draft. A minimum 1 degree draft will ensure that they release from the tool during molding. Rib coring. Core thick ribs from the back or below to create a blank area and thinner rib walls. This will help mitigate cosmetic sinks. Rib radii

Plastic Ribs New Lam
The rib height should not exceed 3 times the bone thickness. The ribs are connected to the molten plastic wall with a 0.5mm (0.02 in) R on both sides to allow for smooth plastic flow and reduce internal stress. PC. The general recommended rib thickness depends on the plastic material flow and wall thickness.

Plastic Ribs New Lam
The following rib design guidelines work well for most plastics materials: Rib thickness at the base should be between 50-70% of the nominal wall thickness. Rib height should be 2.5 - 3X the nominal wall thickness. Ribs should have 0.5 - 1.5 degrees of draft (for ejection). Rib base radii should be 0.25 - 0.4X the nominal wall thickness.
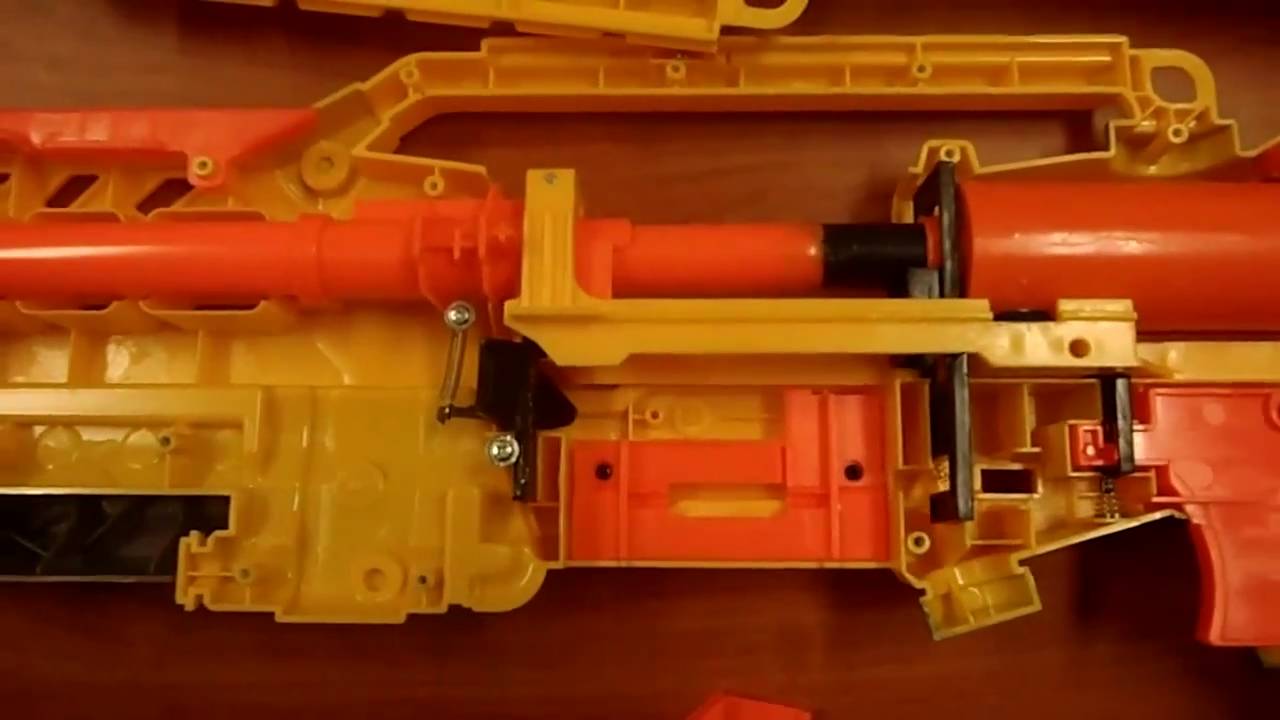
All About Ribs in Injection Moulded Parts Dienamics
When needed, crush ribs can allow for draft and a tight fit for a part that requires both. Figure 1: D-shaped through-hole in center of gear part accepts the drive shaft. Press fits for injection-molded parts can be challenging. A well-designed injection-molded part will usually have draft, but the same draft that helps eject a part from the.
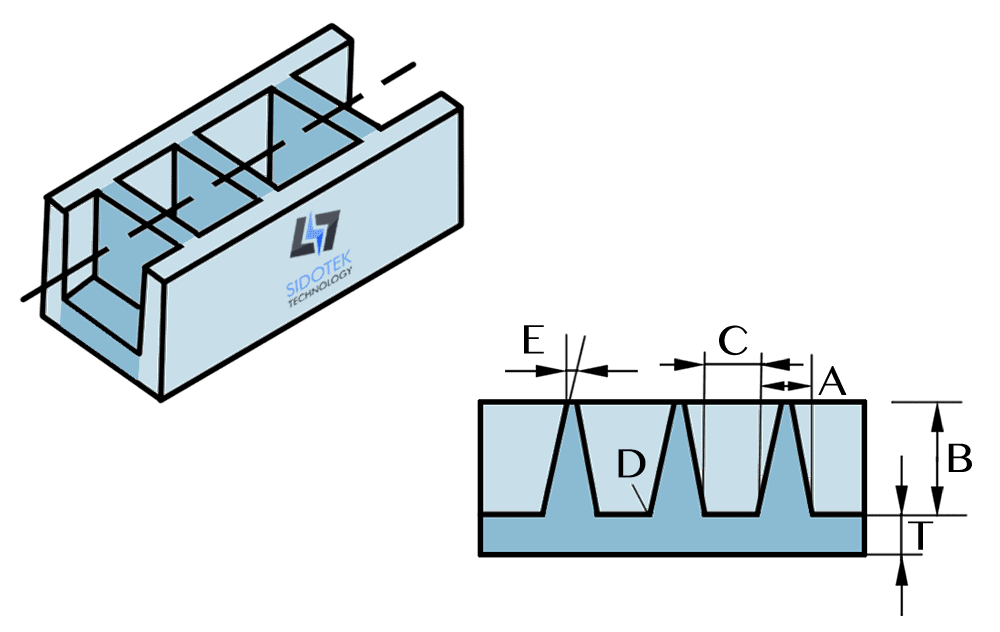
Ribs and Bosses Design Guidelines in Plastic Parts SIDOTEK TECHNOLOGY
Adding plastic ribs. When the normal wall thickness is not stiff enough or strong enough to stand up to service conditions, rather than making the whole wall thicker, the part can be strengthened by adding ribs. The principle is similar to that used in steel girders, where 'I' and 'T' sections are almost as rigid as solid beams, but are only a.
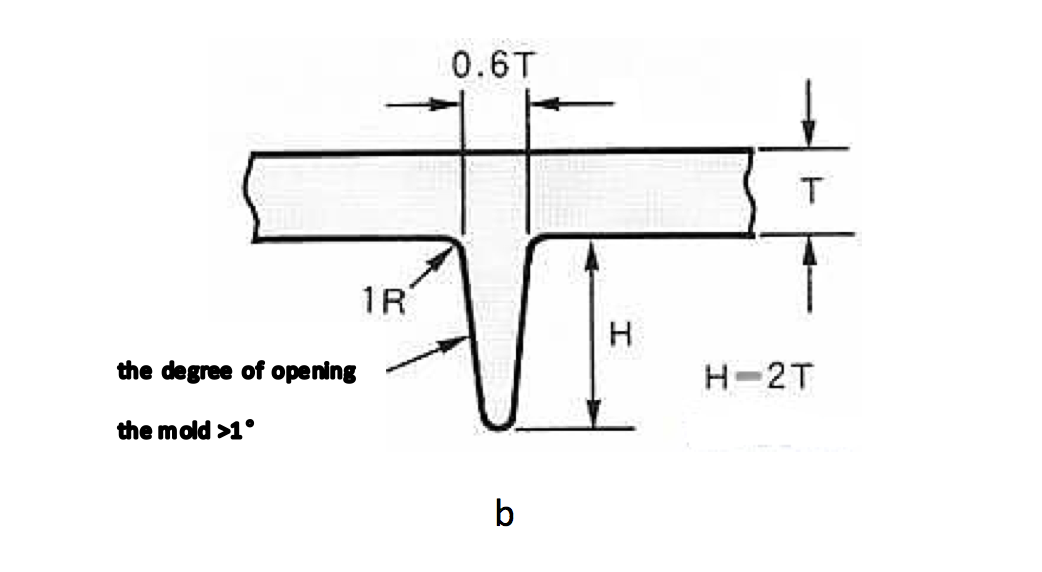
How To Increase The Rigidity of Your Plastic The Rib Design
The Reinforcing Rib structure design on the plastic. The effect of Reinforcing Rib can not only improve the strength and stiffness of plastic products, reduce the distortion phenomenon, but also make plastic molding easy to fill the cavity. As is shown below. 1.1. The design principle of the Reinforcing Rib
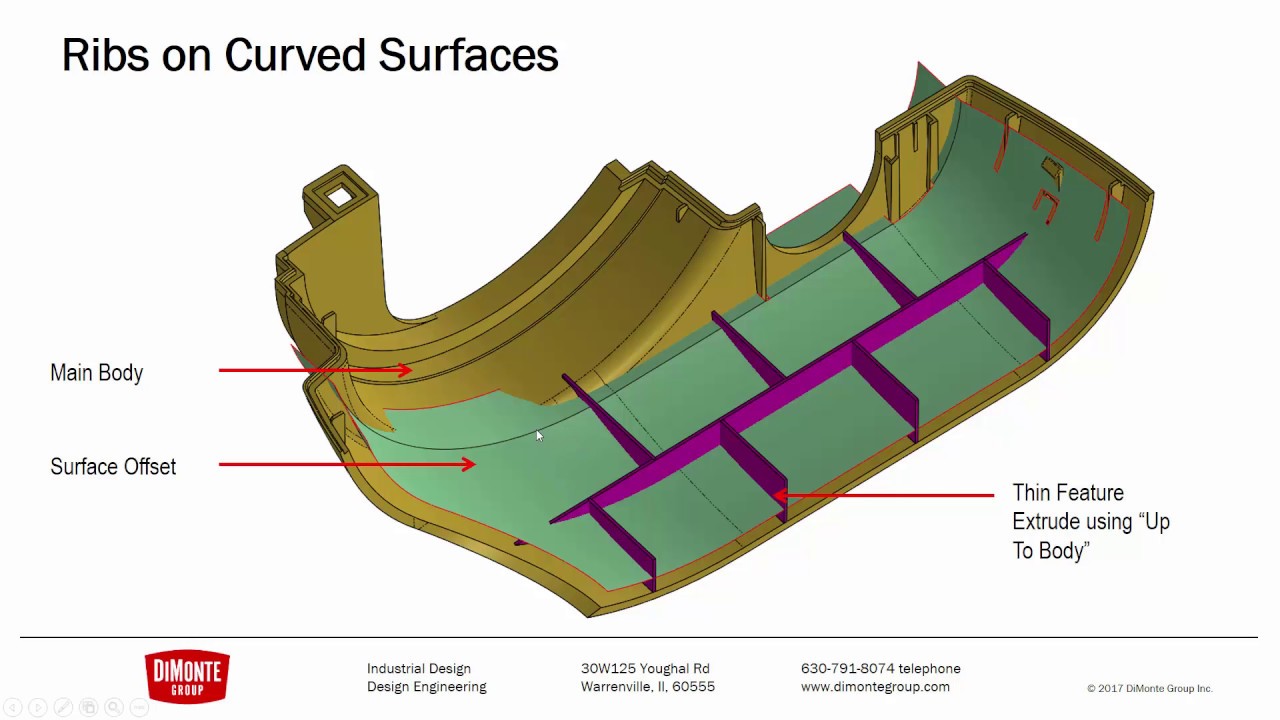
Fantastic Plastic 19 Ribs on Curved Surfaces SOLIDWORKS YouTube
For the easy removal of plastic parts from your injection mold, the draft angle is implemented. The ideal draft angle for the outer rib is 0.5 degrees, while in the inner rib it is 0.25 degrees. In addition to the recommended draft angle, the inclusion of a rib intersection is also advised because it prevents excessive sinking on the rib's.
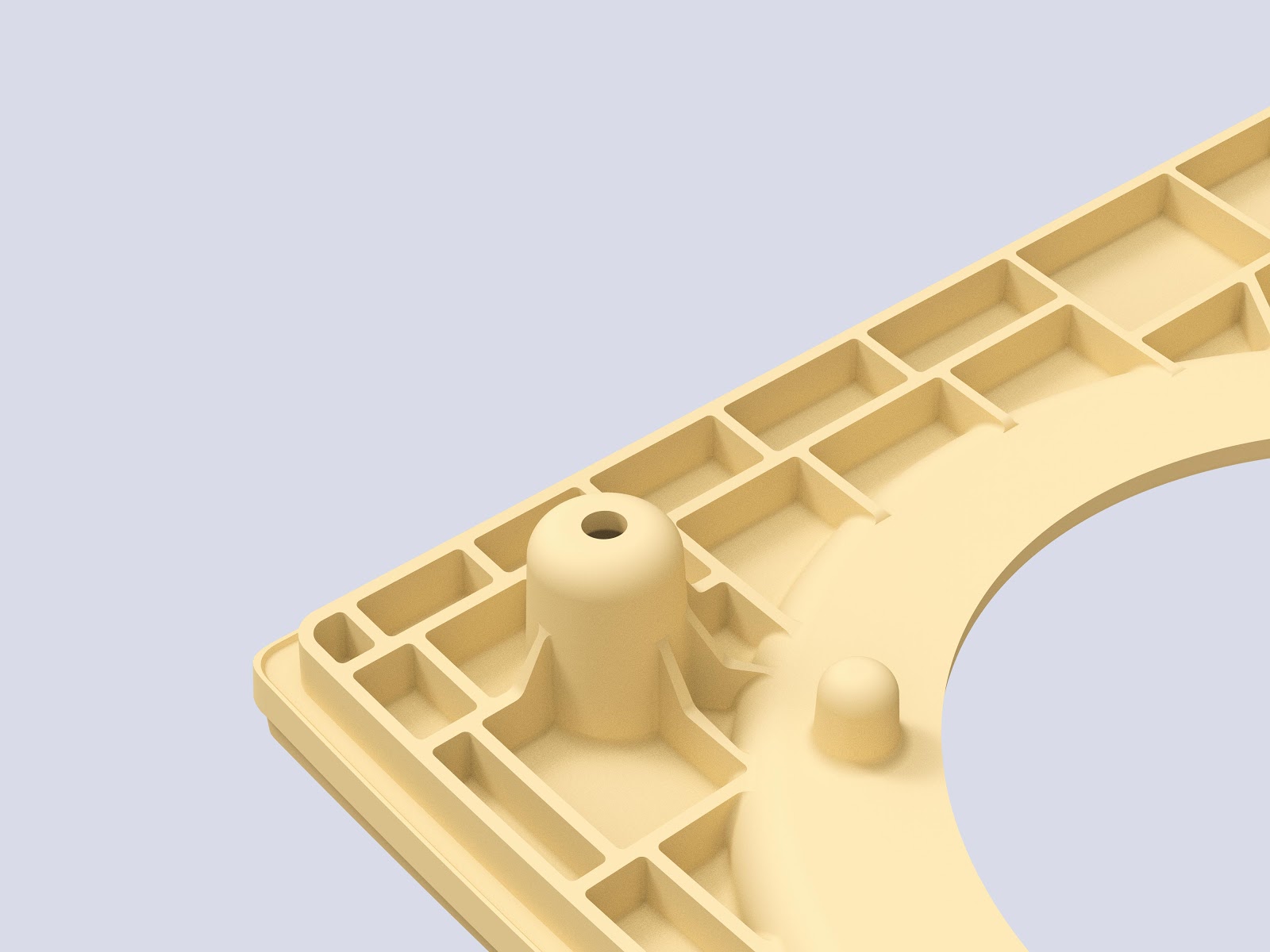
Tips on injection mouldmaking · Precious Plastic Toolbox
Plastic Rib Design. Ribs are thin, wall-like features typically designed into the geometry of a part to add internal support to walls or other features like bosses. In a similar fashion, gussets are support features that reinforce areas such as walls or bosses to the floor. Just as bridge beams and columns are supported at their vertex with.
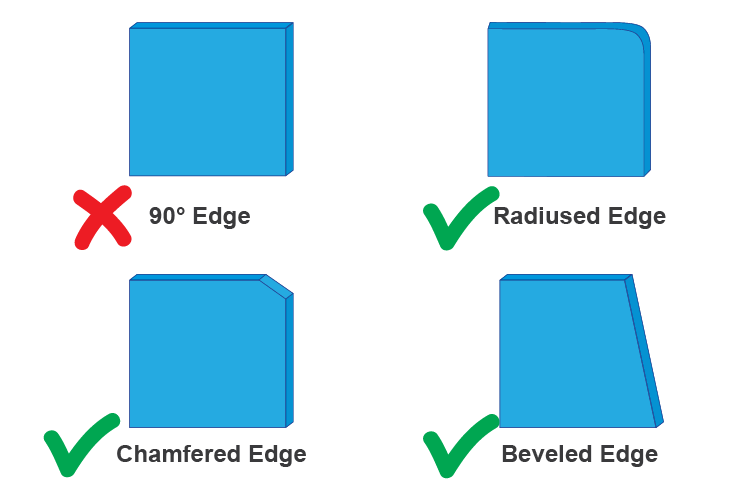
Injection Molding Rib Design 3 Space
Place ribs along thin sections and long, flat sections to add structure and strength. Place ribs a minimum of two to three times the nominal wall thickness apart from each other. Adding excessive ribs can prolong cycle time, increase ejection risks, and increase material use.